Machining
Machining is a technical and detail-oriented process in which material is cut into a final shape and size to create parts, tools, and instruments. Machining is typically used to shape metals, though it can also be used on a variety of other raw materials. Machine shops utilize equipment and tools like mills, lathes, and drill presses to cut material and 3D printers to add material.
What is machining?
Machining is the process used to remove material, typically metal, to create parts for machines, tools, transportation, and more. Machine shops and machinists use equipment like lathes, mills, and drill presses to turn material into useful tools using precise cuts.
What do machine shops do?
Machine shops use equipment and machines to create tools and parts. These parts need to be strategically cut using a high level of accuracy to fit their specific function and fit the machine they will be used in. Machinists remove material from objects that are made of metal, though machining techniques can also be used on wood, ceramic, and plastic materials. Machining is used on engines, bicycles, appliances, kinetic or mechanical projects, and much more.
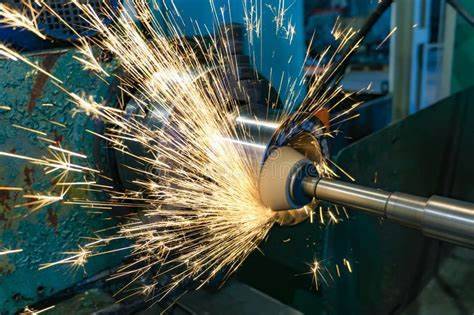

What materials can be machined?
Machining is most commonly used to manufacture metal objects, parts, and tools. Metals that can be machined are stainless steel, aluminum, brass, titanium, and copper. Stainless steel is commonly used for precision machining, offering the advantages of strength and resistance to corrosion. Aluminum is lightweight, easy to work with, and inexpensive. Brass is another economical material used for machining, but should not be used in semiconductor products because of the zinc and tin in the material. Titanium is strong, lightweight, and resistant to corroding, however, it is more expensive than other materials and difficult to work with. Copper is a versatile and strong metal and works well as an electrical conductor. Plastics are also used in machining as they are inexpensive and non-conductive. They are commonly used in medical, electrical, and scientific industries.
Machining techniques
There are two main techniques when it comes to machining operations: subtractive and additive manufacturing. These techniques are used by a machinist to either take away or add material to a part.
Subtractive
Machining is a prototyping and manufacturing process that creates the desired shape by removing unwanted material from a larger piece of material. Since a part is built by taking away material, this process is also known as subtractive manufacturing.
Additive
Additive machining, also known as 3D printing, is a newer approach to production that enables the construction of a three-dimensional object from a digital model. It allows the machinist to create lightweight and strong parts.
Common machine shop tools
There are many types of machining tools, and they may be used alone or in conjunction with other tools at various steps of the manufacturing process. Some tools in a machine shop have very specific purposes, while others are more versatile and can be used for many different uses.
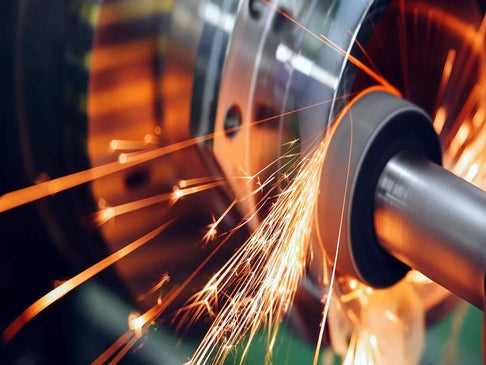
- Cutting tools
Cutting tools in a machine shop include devices like saws and shears. They are used to cut material with specific and predetermined dimensions, such as sheet metal.
- Boring tools
Boring tools are used to enlarge or re-shape an established hole. A machine shop may use a jig borer to accurately locate the precise center of a hole and a horizontal boring machine to perform the cut. Modern machining also uses CNC machines to ensure repeatability throughout a workpiece.
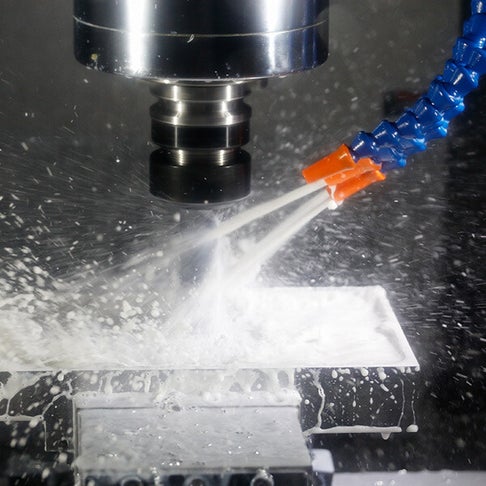
- Drilling tools
Drilling tools are devices that rotate to create round holes on a workpiece by removing material. A machine shop may have a designated drill press for hole making or specific tools that can be attached to compatible machineries such as a lathe or CNC machine.
- Turning tools
Turning tools rotate a workpiece while a cutting tool removes material, shaping it to the desired form. Horizontal lathes are the most common type of turning machine used in a machine shop.
- Grinding tools
Grinding tools use a rotating wheel to make light cuts, sharpen tools, or create a finish on a machined workpiece. Pedestal grinders are commonly used in machining to sharpen cutting functions on turning and milling machines. Grinding tools can also deburr and remove any surface imperfections on a workpiece, creating a smooth finish.
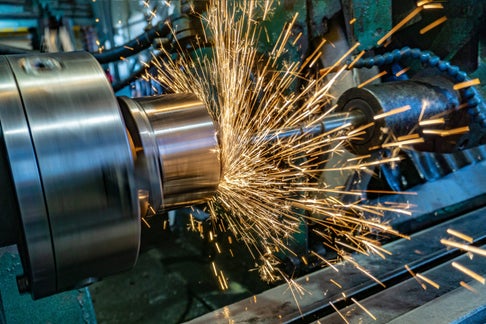
- Milling tools
A mill uses a rotating cutting surface with several blades to create holes or cut designs out of the material. The milling machine is used to mill flat and irregular surfaces, and also to drill, bore, cut, and create slots on a workpiece. The Bridgeport Mill is a brand that became ubiquitous in machine shops around the world.
How to learn machining
It is important to first learn machining from an experienced instructor in an established machine shop. The Company offers machining training and apprenticeships learn the skills needed to drive sharp cutting tools using lathes, milling machines, and drill presses—and make precise, accurate cuts. Our machine shop offers introductory classes for machinists that are just starting out, and open lab time is available for students to perfect their machining skills and for experienced workers to work on personal projects.