Digital Twins
Digital twins in manufacturing refer to virtual replicas of physical products, processes, or systems that exist in the digital realm. They are created by integrating real-time data from various sources such as sensors, equipment, and software, and then using advanced technologies like simulation, analytics, and machine learning to create a digital representation that mirrors the behavior and characteristics of the real-world counterpart.
Digital twins have several important uses in manufacturing:
Product Design and Development: Manufacturers can create digital twins of products during the design phase. This allows them to simulate how the product will behave under various conditions, optimize its performance, and identify potential issues before physical production begins.
Process Optimization: Digital twins can be used to model and simulate manufacturing processes. By analyzing real-time data and running simulations, manufacturers can optimize processes for efficiency, reduce downtime, and minimize waste.
Predictive Maintenance: Digital twins can monitor the health and performance of equipment in real-time. By analyzing data from sensors and comparing it with the digital twin's model, manufacturers can predict when maintenance is required, preventing unexpected downtime and reducing maintenance costs.
Quality Control: Manufacturers can use digital twins to monitor the quality of products during production. By comparing real-time data with the expected behavior in the digital twin, deviations can be quickly identified and addressed, ensuring consistent product quality.
Supply Chain Management: Digital twins can be extended to represent the entire supply chain. This enables manufacturers to monitor and optimize the movement of materials, products, and resources throughout the supply chain, improving coordination and efficiency.
Training and Simulation: Digital twins can serve as training tools for operators and technicians. They can simulate various scenarios and allow personnel to practice operating machinery, troubleshooting issues, and responding to emergencies in a virtual environment.
Continuous Improvement: By analyzing data from both the physical world and the digital twin, manufacturers can identify areas for improvement, implement changes, and then monitor the impact of those changes in a controlled manner.
Customization and Personalization: Digital twins can help manufacturers create customized and personalized products by modeling various configurations and options, enabling them to meet individual customer preferences and requirements.
In essence, digital twins provide manufacturers with a virtual platform to gain insights, optimize operations, and innovate without the need for physical experimentation. They offer a powerful way to bridge the gap between the physical and digital worlds, leading to improved efficiency, reduced costs, and enhanced competitiveness in the manufacturing sector.
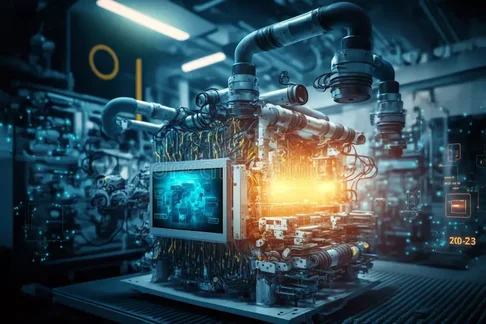
Digital Twins enhance engineering design and manufacturing.
Digital twins are revolutionizing engineering design and manufacturing by creating virtual replicas of physical assets, processes, and systems. These virtual models are not just static representations; they are dynamic and continuously updated with real-time data from their physical counterparts. This allows engineers and manufacturers to gain valuable insights, optimize processes, and make informed decisions throughout the product lifecycle.
Here's how digital twins are being used by the company to for transforming engineering design and manufacturing:
Enhanced Design and Simulation: Digital twins enable engineers to create detailed virtual prototypes of products and systems.
These prototypes can be simulated and tested under various conditions, allowing engineers to identify potential design flaws and optimize performance before physical production begins.
This reduces the need for costly physical prototypes and accelerates the design process.
Improved Manufacturing Processes:
Digital twins can be used to model and simulate entire manufacturing processes. By analyzing real-time data from production equipment, manufacturers can identify bottlenecks, optimize workflows, and improve overall efficiency.
Digital twins can also be used to predict and prevent equipment failures, reducing downtime and maintenance costs.
Predictive Maintenance:
Digital twins can monitor the condition of physical assets in real-time. By analyzing data from sensors and other sources, digital twins can predict when maintenance will be required, allowing manufacturers to schedule maintenance proactively and avoid costly breakdowns.
Product Lifecycle Management:
Digital twins can track products throughout their entire lifecycle, from design and manufacturing to operation and end-of-life.
This provides valuable insights into product performance, usage patterns, and potential areas for improvement.
Digital twins can also be used to support product upgrades and customization.
Collaboration and Communication:
Digital twins can facilitate collaboration and communication between different stakeholders, including engineers, manufacturers, and customers.
By sharing a common view of the digital twin, our engineers can work together more effectively to solve problems and make decisions. Some examples of Digital Twin Applications:
Aerospace: Digital twins are used to design and simulate aircraft, optimize manufacturing processes, and monitor the performance of aircraft in service.
Automotive: Digital twins are used to design and test vehicles, optimize production lines, and develop autonomous driving systems.
Healthcare: Digital twins are used to create personalized treatment plans for patients, optimize hospital operations, and develop new medical devices.
Energy: Digital twins are used to monitor and optimize the performance of power plants, wind turbines, and other energy infrastructure.
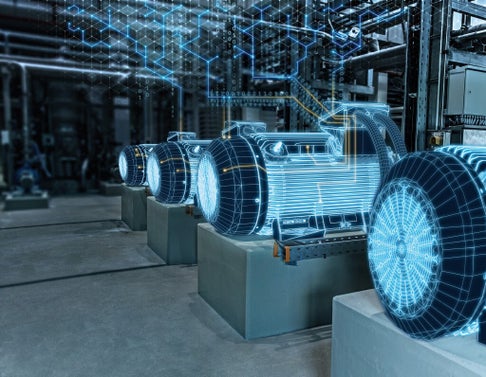
Using digital twins in manufacturing, offers several benefits:
Improved Design and Development: Digital twins enable iterative design and testing in a virtual environment. This results in faster and more accurate product development, as potential issues can be identified and resolved before physical production starts.
Reduced Time-to-Market: With the ability to simulate and optimize processes, manufacturers can bring products to market more quickly. This is because potential bottlenecks and inefficiencies can be addressed early in the design phase.
Cost Savings: Digital twins help identify opportunities for cost reduction by optimizing processes, minimizing waste, and preventing unexpected downtime through predictive maintenance.
Enhanced Product Quality: By continuously monitoring and comparing real-time data with the digital twin's expected behavior, manufacturers can maintain consistent product quality and identify deviations for prompt corrective action.
Predictive Maintenance: Digital twins allow for real-time monitoring of equipment health and performance. Predictive maintenance based on digital twin insights helps reduce unplanned downtime and extends the lifespan of equipment.
Optimized Operations: Simulating processes and systems in a digital twin environment allows for better process optimization, resulting in increased operational efficiency and resource utilization.
Risk Reduction: Manufacturers can test and validate scenarios in a virtual environment before implementing them in the real world, reducing the risk of failures and unexpected consequences.
Data-Driven Insights: Digital twins generate vast amounts of data that can be analyzed to gain insights into operations, performance, and customer behavior. This data-driven approach supports informed decision-making.
Remote Monitoring and Control: Digital twins enable remote monitoring and control of equipment and processes, allowing for real-time adjustments and interventions, even from a distance.
Sustainability and Environmental Impact: By optimizing processes and reducing waste, digital twins contribute to more sustainable manufacturing practices, helping to minimize environmental impact.
Training and Skill Development: Digital twins provide a safe and controlled environment for training personnel, allowing them to learn and practice operating machinery, troubleshooting issues, and responding to various scenarios.
Innovation and Experimentation: Manufacturers can use digital twins to experiment with new ideas, configurations, and strategies without disrupting ongoing operations. This encourages innovation and the exploration of new opportunities.
Customization and Personalization: Digital twins enable the creation of customized products by simulating different configurations and options, catering to individual customer preferences.
Supply Chain Optimization: By extending digital twins to cover the entire supply chain, manufacturers can optimize the movement of materials, products, and resources, leading to better coordination and efficiency.
Continuous Improvement: Digital twins provide a feedback loop for ongoing improvement. By analyzing data from both the digital and physical realms, manufacturers can implement changes and monitor their impact over time.
Digital twins offer a wide range of benefits that contribute to improved efficiency, reduced costs, enhanced product quality, and increased competitiveness across industries.