Ikiga Manufacturing Technologies
Technologies, products and processes to improve manufacturing performance.
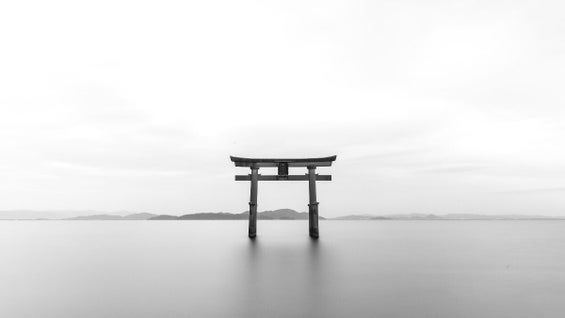
Ikigai is a concept that has been deeply embedded in Japan’s cultural tapestry for centuries. It translates to “reason to live,” but its significance extends far beyond its literal meaning.
Ikiga embodies a way of life without ostentatious displays of pride or self-aggrandizement. It was chosen as the name of Avant-Garde-Technologies Corporation's manufacturing subsidiary, because ikigai defies all boundaries or stipulations. It is a holistic, all-encompassing concept that transcends any prescribed framework.
Ikiga Manufacturing represents a business segment that was created to facilitate Industrial IoT (IIoT). The Company has over 200 of the best industrial engineers as well as over 40,000 engineers and scientists in other technology fields. It places great emphasis on improving manufacturing. This innovation is the result of designing new equipment, robotics, software applications and AI Deep Learning.
Manufacturing is very diversified and depends upon the products being manufactured when designing equipment and software. Although manufacturing has been done for thousands of years, modern methods of manufacturing are in their infancy. The company is putting large amounts of resources in manufacturing innovations that will enable manufacturing companies to achieve much greater performance, profitability, quality and economies of scale.
Manufacturing is the making of goods.
The items that are manufactured may be completed products or they might consist of components that contribute to a whole that's produced in another facility. Manufacturing facilities typically feature production lines or areas that are dedicated to producing one or more items. A facility might manufacture products to stock stores or make them to order, producing items only as they're requested by a buyer. The manufacturing industry is essential for the production.
Types of manufacturing
Manufacturing environments may be categorized by product or process. These classifications will help you understand how a facility operates.
Types of factories
There are three primary types of factories for manufacturing operations. The type of factory operations that are in place depends upon the product or selection of products that are produced as well as the demand for them.
- Repetitive assembly line
In a repetitive manufacturing plant, assembly lines produce a single item multiple times. The machinery is calibrated for only one product and the line operates faster or slower depending on the consumer demand for the product. A second assembly line may open seasonally as demand requires.
- Discrete assembly line
In a discrete manufacturing environment, the production line may produce a variety of items. The machinery facilitates convenient changeovers. There is more downtime in this environment, as tear-down and set-up must take place between different batches.
- Job shop
A job shop uses production areas rather than assembly lines. These areas may produce one item or many. A job shop has more labor operations than automated machinery, and typically produces fewer items than either a repetitive or discrete assembly line.
Different types of manufacturing
The manufacturing industry is extremely diverse. These factories are responsible for producing nearly everything that consumers purchase. The primary types of industrial factories are:
Petroleum, chemicals and plastics
This segment of the industry turns crude oil into plastic products and transforms coal and chemicals into items like paint, pesticides or soaps. This industry also facilitates the production of rubber.
Food
Food manufacturing includes everything from canned goods and processed dry goods to fresh or frozen produce. Canning and packaging are a major part of this type of production process.
Clothing and textiles
The clothing and textile industry turns cotton, flax and wool into apparel, bedding and home goods. However, products that are made from synthetic materials are considered part of chemical manufacturing rather than textiles, even when the end product is still a piece of clothing. Seamstresses and tailors often work in these production lines.
Metal
Metal manufacturing includes all products made from aluminum, iron or steel. These production lines incorporate forging, stamping and coating activities.
Electronics
The electronics sector includes appliances, computers and all types of audio-visual equipment.
Transportation
Transportation manufacturing includes the production of motor vehicles, boats, ships, trains and aircraft as well as the engines and parts that go into them.
Wood and paper
The manufacturing of wood and paper includes wood materials such as lumber and various paper products made from wood pulp.
Most Common Manufacturing Processes:
Casting: This process involves pouring molten material (such as metal, plastic, or ceramic) into a mold, allowing it to cool and solidify into the desired shape. Casting is used to create complex geometries and is often employed for large parts like engine blocks or sculptures.
Machining: Machining involves removing material from a workpiece to achieve the desired shape. Techniques like turning, milling, drilling, and grinding are used to create precise components with tight tolerances. Computer Numerical Control (CNC) machines automate these processes.
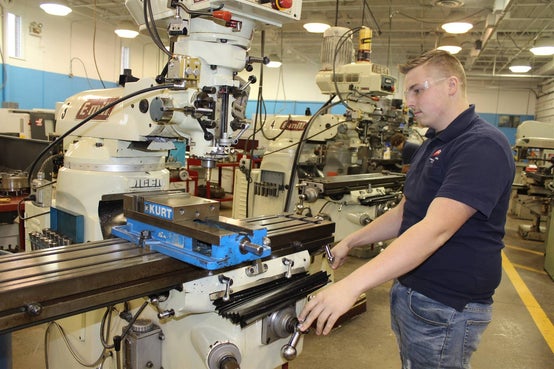
Forming: Forming processes include techniques like rolling, forging, and stamping, where material is reshaped without removing any significant material. These methods are commonly used for producing sheet metal components, fasteners, and automotive parts.
Joining: Joining processes involve combining multiple parts into a single assembly. Techniques like welding, soldering, brazing, and adhesive bonding are used to create strong and durable connections between materials.
Additive Manufacturing (3D Printing): This is a revolutionary process that builds objects layer by layer from digital designs. It's particularly useful for creating complex, customized, or intricate parts. Various materials such as plastics, metals, and ceramics can be used.
Injection Molding: This process is widely used for mass-producing plastic parts. Molten plastic is injected into a mold, cooled, and then the mold is opened to release the solidified part.
Extrusion: Similar to injection molding, extrusion is used for creating long continuous shapes, such as pipes, tubes, and profiles. Material is pushed through a die to form the desired shape.
Powder Metallurgy: This process involves compacting metal powders into a desired shape using high pressure, followed by sintering (heating the compacted powder) to achieve bonding and densification.
Machining processes
Machining is the process of removing material on a workpiece in order to create a precise object or part. The following are the primary processes used to cut and subtract material in a machine shop by a machinist.
Turning
Turning is a process that rotates the workpiece as the primary method of moving metal against the cutting tool. Lathes are the principal machine tool used in turning.
Milling
Milling uses a rotating cutting tool to bring cutting edges to bear against the workpiece. This is the most versatile tool and technique used in a machine shop.
Drilling
Drilling creates a new hole or refines an existing hole using a rotating cutter. Drilling is most commonly done using drill presses, but sometimes drilling tools will be attached to compatible lathes or mills to create holes.
Boring
Boring is one of the most widely used techniques in machining, as it is one of the most reliable ways to finish and enlarge pre-existing holes. This technique provides accuracy and is easily replicated on a workpiece.
Reaming
Reaming is a process that uses a rotary cutting tool to smooth an existing hole in a workpiece. This is a cutting process that removes material, and its primary purpose is to even out the walls of a hole.
Future Manufacturing Technologies:
Advanced Robotics: Collaborative robots (cobots) and autonomous robots are being integrated into manufacturing to enhance efficiency, safety, and flexibility. They can perform tasks like assembly, packaging, and even intricate operations with high precision.
Smart Manufacturing and Industry 4.0: The integration of IoT (Internet of Things), sensors, data analytics, and AI into manufacturing processes is enabling real-time monitoring, predictive maintenance, and optimization of production workflows.
Digital Twins: These are virtual replicas of physical objects or processes. In manufacturing, digital twins allow for simulation, analysis, and optimization of production processes, leading to reduced downtime and improved quality.
Nanotechnology: The manipulation of materials at the nanoscale level is opening up possibilities for creating novel materials with enhanced properties, such as increased strength, conductivity, and durability.
Biomanufacturing: This involves using living cells, bacteria, or microorganisms to produce materials like proteins, enzymes, and even tissues. It has applications in pharmaceuticals, biomaterials, and regenerative medicine.
Advanced Materials: The development of new materials, such as superalloys, composites, and smart materials, is revolutionizing manufacturing by providing materials with superior properties, like higher strength-to-weight ratios or self-healing capabilities.
Green Manufacturing: Sustainable and environmentally friendly manufacturing practices are gaining importance. Technologies like energy-efficient processes, recycling, and reduced waste generation are being adopted to minimize the ecological footprint of manufacturing.
Quantum Computing: Although still in its infancy, quantum computing holds potential for solving complex optimization and simulation problems, which could greatly benefit manufacturing processes and supply chain management.
Advanced Additive Manufacturing: Research continues to expand the capabilities of 3D printing, including multi-material printing, faster printing speeds, and the use of new materials like metals and ceramics.
Augmented Reality (AR) and Virtual Reality (VR): These technologies are being utilized for training, maintenance, and design review in manufacturing. They can enhance worker skills, facilitate remote assistance, and aid in visualizing complex assembly processes.
These manufacturing processes and future technologies are continuously evolving, driven by the need for increased efficiency, reduced waste, and the exploration of innovative materials and techniques.